Commitment to Quality
Excellent ceramic former technology always exists at the foundation of excellent manufacturing.
We recognize that the rubber products made by our customers are our "finished products," and we provide ceramic formers with this sense of responsibility.
We aim to improve quality control in our manufacturing processes while continuing to conduct research so that we can be of service at our customers' manufacturing sites.
1. Research and development of raw materials
We also independently develop raw materials for former manufacturing. In this way, we strive to improve the quality of our products.
- We are improving thermal shock strength to support "rapid heating and rapid cooling."
- Increase physical strength of product.
- Enhance abrasion and chemical resistance.
- We ensure the uniformity and consistency of our products.
2. Former shape and design
We study the shapes and designs of the formers that are used on our customers' production lines to improve the quality of products.
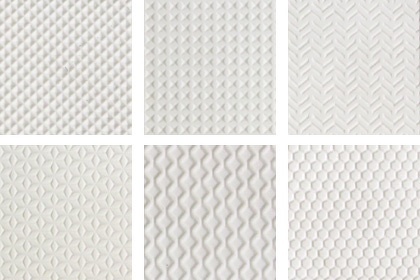
Example of palm pattern
- Wearability of gloves.
- Conformity to glove production line design.
- Easy stripping of gloves or other dipping products.
- Well-designed formers may reduce manufacturing problems that may occur in the dipping process.
3. Surface processing of formers
Treating the surfaces of formers produces the following additional effects:
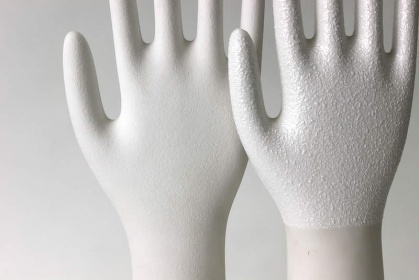
Example of surface treatment
- Film uniformity can be achieved through coating of the former surface.
- Thickness adjustment that is suitable for each material such as latex and nitrile.
- Engraved pattern for better grip.
- Enhance cleaning effect.
4. Product quality control
In order to maintain the product quality of our customers, our products are managed as follows:
- Thickness of ceramic formers is controlled.
- Inspection of ceramic former’s dimensions.
- Water absorption rate 0% Complete porcelain.
- Crack and pinhole inspection.
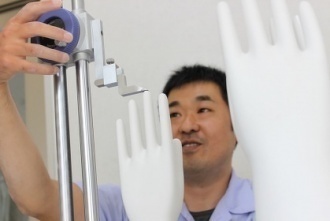